Today we BLMA will share with you about what needs to be paid attention to when discharging and refueling the hydraulic pipe bender system.
Regularly filter water and sediment from the hydraulic tube bender tank, which is critical to removing impurities from the oil. At the same time, the oil in the entire hydraulic system must be emptied regularly. This is to completely remove system impurities, oxidized hydraulic oil and other harmful substances. After completion, the cleaned hydraulic oil needs to be re-added to the system.
Because good quality hydraulic oil contains a variety of additives, these additives can prevent oil from spoiling or clogging system parts. But after a long period of use, no one can guarantee its effectiveness. Therefore, it needs to be replaced regularly. In addition to draining and refueling, regular filter replacement is also one of the measures to keep the hydraulic pipe bender system clean in order to keep the system clean.
Introduction of hydraulic system in tube bending equipment for sale
Hydraulic pipe bender is mainly powered by hydraulic system. Let's introduce what constitutes a hydraulic system. An oil circuit control board (also called oil circuit board), four or five groups of solenoid valves, each group of solenoid valves control one action unit. Generally, there are four groups of clamping, core pulling, auxiliary pushing and bending. Because each part of the action is independent, it needs to be controlled by a separate solenoid valve. A group of pressure-holding valves: pressure-holding valves are used for clamping. Because when the pipe is bent, it will be subject to expansion force. If there is no pressure maintaining valve to keep the oil pressure stable, there will be clamping and unable to clamp, and wrinkling and deformation will occur when the pipe is bent.
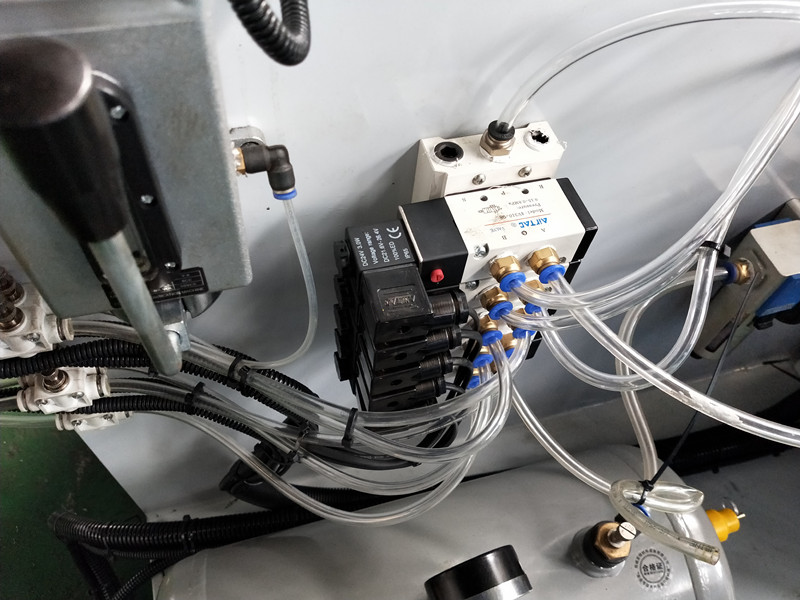