Maintenance of pipe bending machine
1. Daily maintenance (first-level maintenance):
Before boot
1).Check whether there is any debris on the machine and whether there is any obstruction within the effective range of the machine, and remove it.
2).Check whether the hydraulic pressure meets the current requirements, and adjust the pressure according to the needs of the elbow.
3).Choose the appropriate mold according to the pipe material: wheel mold, guide mold, main clamp, material clamp, etc., and fasten them according to the assembly requirements.
4).Check whether the emergency stop device is sensitive and reliable, otherwise, report for repair.
5).Turn on the control system, enter the pipe bending system, first reset the hardware and software to zero at the same time, and check whether the button of the emergency stop device is reliable.
Figure 1 BLMA CNC pipe bender
At work
According to the current actual bending requirements, write the appropriate parameters: elbow length, elbow angle, tilt angle, interval length, etc.,
Select "Semi-Auto Mode" for pipe bending. Run empty, observe the encoder angle feedback value and servo travel distance feedback
1).Manual feeding, after the clip is tightened, the person immediately leaves the machine operating area until the end of the operation to avoid bumps.Automatic feeding,operator should leave before the processing.
2).During operation, if there is any accident, it will stop immediately.
After work
1).Reset the machine to zero, turn off the power of the system and the machine, and store the power-on key in the tool box.
2).Clean the dust and iron filings of the machinery and equipment, add a little lubricating oil to the track, and cover the industrial computer with a dust cover.
3).Clean the sanitation of the work area and keep the remaining waste from the work out of the waste bin.
2 .Secondary maintenance (before weekends or holidays)
1).Open the cover of the industrial computer, and use dry compressed air to clean the dust inside the machine, especially in summer, it is extremely important, which may affect the normal operation of machinery and equipment.
2).Clean the oil in the control box, check whether the hydraulic oil leaks in the hydraulic control box, and whether the pressure has dropped significantly.
3).Replace the three-hole plate, two-hole plate, wear-resistant plate, blocking shaft and related bearings according to the wear and tear of the machine and equipment.
4).The cylinder sealing ring is replaced once a year, the pump body valve group is cleaned and replaced.
5).Proximity switch detection and replacement of electrical parts, detection of servo system and running test of system software once a year.
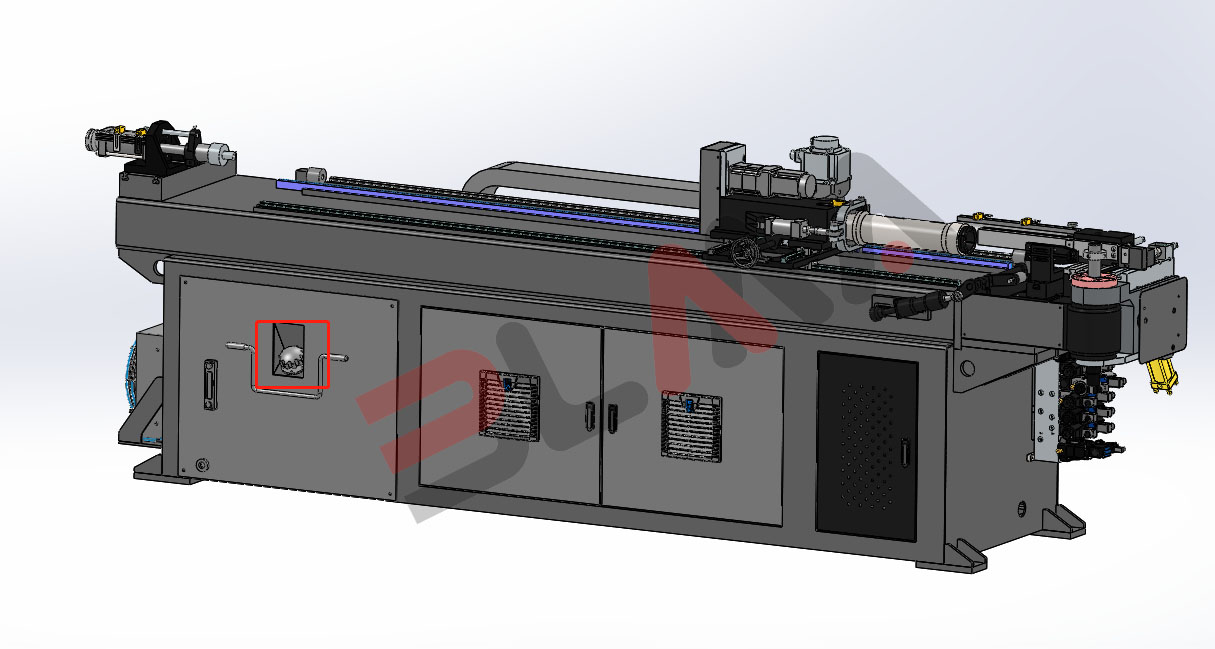
Figure 2 Tank filler